Next-Gen Automotive Software Testing With Corellium And Vector SIL Kit
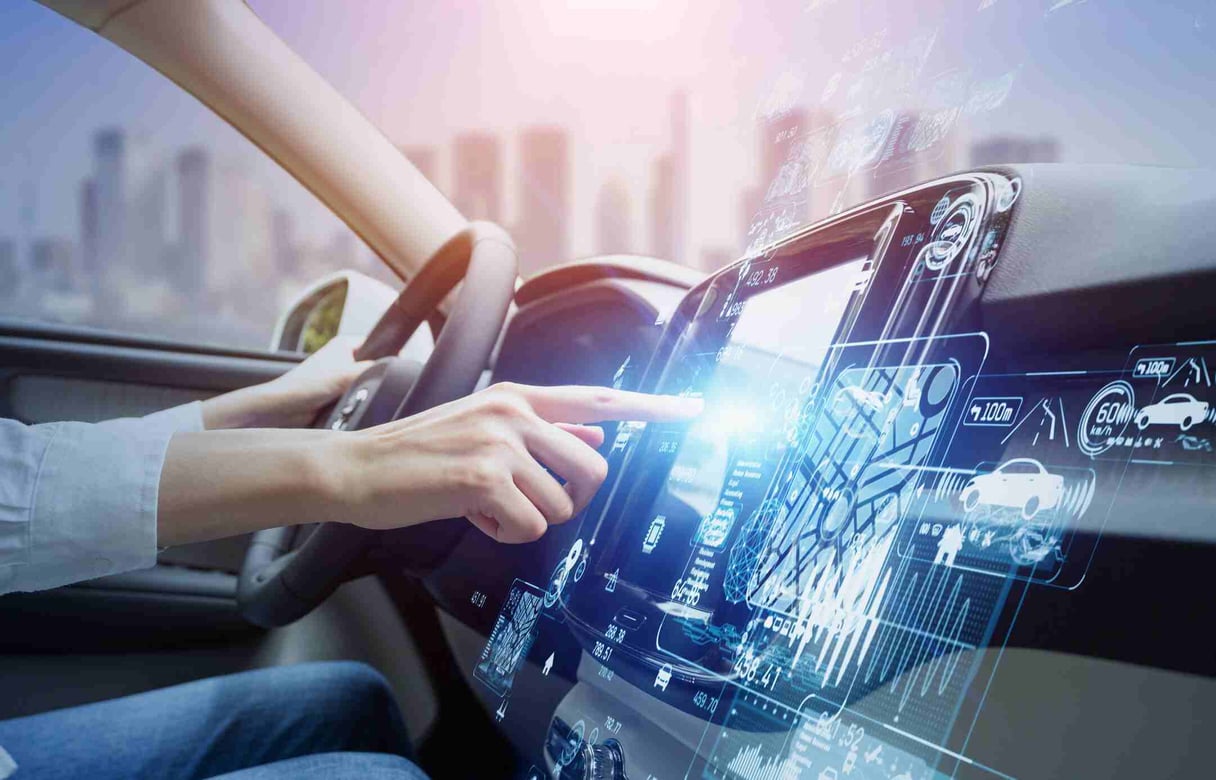
“The automotive industry is confronting a widening and unsustainable gap between software complexity and productivity levels,” opines a McKinsey study. As automotive software requirements continue to increase rapidly, OEMs and suppliers cannot step up their productivity to accommodate newer innovations — resulting in lagging productivity.
Corellium’s Bill Neifert and Vector’s Markus Helmling expound on how real-time virtual devices (along with software-in-the-loop testing environments) can be used to accelerate automotive software testing and development cycles. Register to watch the entire on-demand webinar.
Adopting Cloud Methodologies Will Advance Automotive Software
Using virtual devices instead of sensors, PCBs, and other expensive IoT devices will allow your teams to move their software development workflows to the cloud, resulting in cost-effective and rapid automotive software testing, development and deployment cycles.
Adopting cloud-based software development methodologies has allowed other industries to solve complex problems. However, the automotive industry has yet to fully embrace this paradigm.
For instance, even today, changing to a software module installed on a hardware component involves a lot of work. Limitations like software backward compatibility, physical shipping of components, and damages continue to stall our software development processes.
But using virtual models that mimic the real-time performance and attributes of automotive hardware components offers the following benefits:
- Accelerated cloud-based software development by up to 2 years
- Control as many devices as needed via API calls
- Start development without the hardware
- Better collaboration across global teams
- Instant global deployment of changes
- Greater visibility and control of costs
Corellium Supports Accurate and High-Performance Virtualization
The Corellium type 1 Hypervisor for ARM (CHARM) runs directly on powerful physical ARM servers to support virtualized device development. As a result, Corellium can run the same binaries and binary paths as your actual hardware. So, there is no modeling ambiguity.
Corellium also maps processors one-to-one to the underlying server processors. So you can scale the virtual model as required by your design. Because the virtual model executes on par with (and at times exceeds) real-time speeds, you don't experience any lags.
Recently, ARM launched its own auto-enhanced IP product to support automotive software testing. Corellium fully supports ARM virtual hardware and FVP technology for app development.
Vector CANoe and SIL Kit Improves Automotive Software Testing
Vector offers a wide range of automotive products from embedded software to testing toolkits. In this context, we’re interested in two products namely Vector CANoe and Vector SIL Kit.
- Vector CANoe is an automotive software testing product that helps teams perform real-time tests. Alongside analysis, logging, and measurement tools, the product also features a test executor and an environment simulator.
- Vector SIL Kit is an open-source middleware library that connects Vector CANoe to any test tool, simulator, emulator, virtual ECU, or software.
In the on-demand webinar, our guest Markus takes you through a step-by-step live demo of setting up a CAN network via a VPN to create virtual models of an automotive engine and light.
Seamlessly Run Mixed Critically (ASIL) Workloads on Corellium
The ISO 26262 standard defines four Automotive Safety Integrity Levels (ASIL) - A, B, C, and D. ASIL A represents the lowest degree of threat to humans, while ASIL D represents the highest degree of threat.
Automotive systems like airbags and braking fall under ASIL D, while a lesser critical system such as cruise control falls under ASIL C. Headlights and brake lights fall under ASIL B. And rear lights fall under ASIL A.
Naturally, systems under the ASIL D and C levels undergo more scrutiny than lower-level systems. For instance, you must subject your braking system to formal analysis and fault injections, run it on a certified RTOS, and have error correction codes (ECC).
However, subjecting all your existing software processes to meet such ASIL D requirements will strain your development resources. So a typical approach is to use containers, hypervisors and separate processor subsystems to isolate workloads.
Corellium’s virtual hardware model allows you to run mixed-criticality workloads without increasing complexity. For example, you can run all ASIL C and D systems on a dedicated real-time core while you run all the ASIL A and B systems on a separate core. Nested hypervisors and containers are also supported so you can run your mixed critical software loads on the virtual model the same way you would on the actual hardware.
In the on-demand webinar, Bill explains how to run such mixed criticality workloads on Corellium’s soon-to-be-released Arm RD-1AE System and Open AD Kit. He also gives a demo of running a mixed criticality workload by running Autoware on an EC2 Instance AWS Graviton3 processor, while it communicates over Ethernet to a Corellium virtual cloud model.
Watch the entire on-demand webinar to learn how to accelerate automotive software development and testing using virtual devices and Software-in-the-Loop environments.
Revolutionize Your IoT Device DevOps with Corellium
Modernize the development of your IoT embedded software and companion mobile apps with virtual devices that tie into your SDLC process. Learn how Corellium’s high-precision virtual models enable faster development, enhanced security, and lower costs.
Book a meeting to learn how Corellium accelerates software development lifecycles with Arm-native virtual models and powerful tools and APIs.
Keep reading
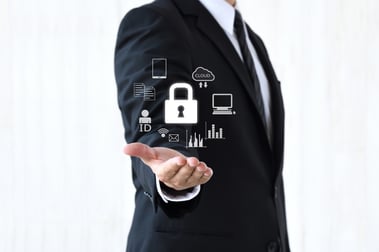
Employee Spotlight: Brian Robison, Chief Evangelist and VP of Product at Corellium
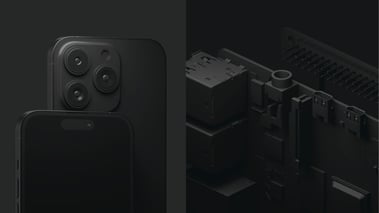
Advancing Automotive Software Development and Mobile Security Testing with Corellium
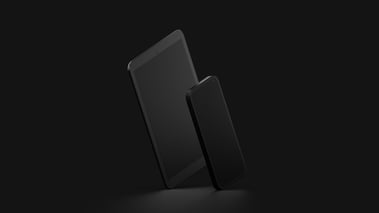